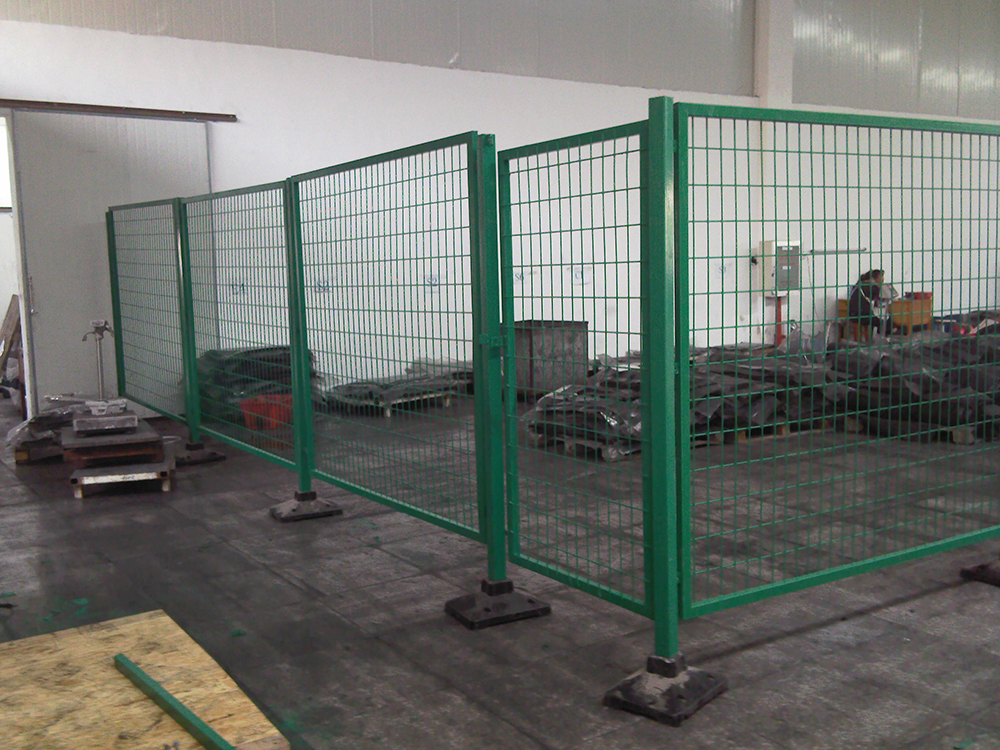
一、引言:传统车间隔离痛点凸显,柔性生产催生可移动隔离网需求
在智能制造升级浪潮中,车间布局需随订单量、产品线动态调整。传统固定式隔离网面临三大难题:
- 安装周期长:焊接式隔离网安装需 3-5 天 / 100㎡,影响正常生产;
- 调整成本高:重新切割焊接导致材料浪费率达 20%,搬迁损耗超 30%;
- 空间僵化:固定分区无法适应小批量多品种生产模式,设备动线优化困难。
某电子厂数据显示,使用可移动隔离网后,车间重组时间从 48 小时缩短至 6 小时,产能利用率提升 15%。这种 “即装即调” 的柔性解决方案,正成为制造业降本增效的关键抓手。
二、传统隔离网 VS 可移动隔离网:三大核心优势对比
某汽车零部件车间案例:原使用固定式隔离网,每次产线切换需停产 2 天,损耗达 5 万元;改用可移动隔离网后,通过轨道滑轮系统实现 1 小时内快速移位,年节省成本超 30 万元。其核心优势在于模块化设计:所有部件标准化生产,支持现场快速组装,无需专业工具,普通工人即可操作。
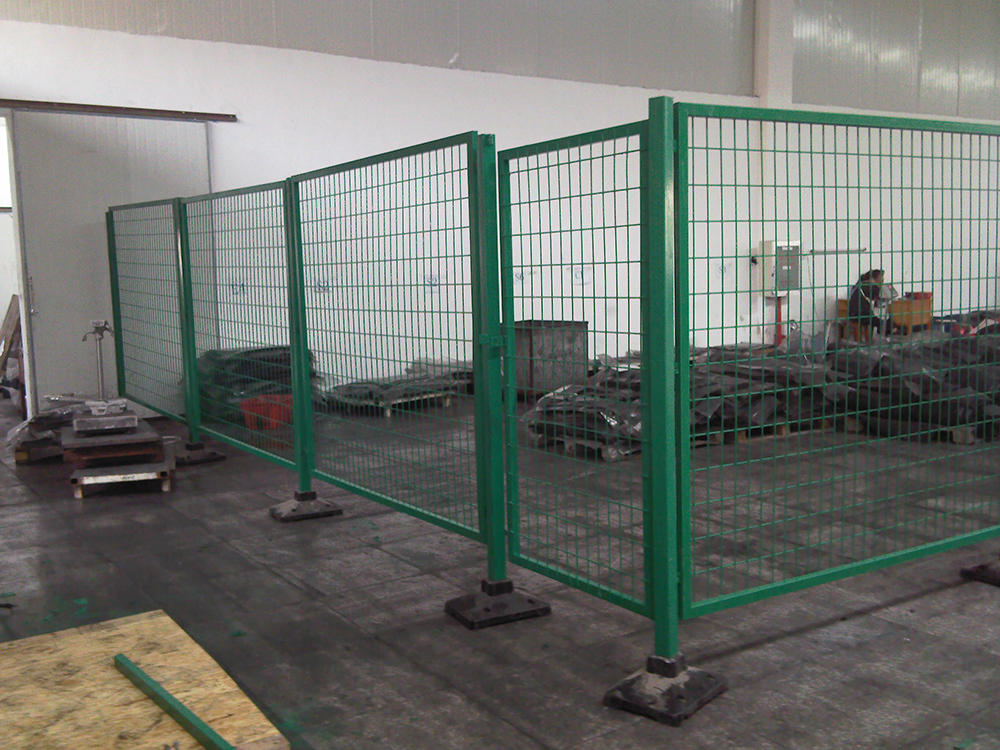
三、可移动隔离网的三大技术突破,实现 “安装即灵活”
采用专利设计的 ABS 工程塑料卡扣,支持 ±15° 角度调节,适配不规则车间地形。某仓储物流中心利用该设计,在弧形通道区域实现无缝隔离,空间利用率提升 22%。
底部配置高精度轴承滑轮,单轨承重达 200kg/m,推动阻力<50N(相当于拎起 5kg 重物);搭配脚踏式刹车,定位精度≤2mm,满足精密设备区域的稳定隔离需求。
基材采用 275g/㎡热镀锌钢板(国标 GB/T 2518),外覆 0.8mm 厚度 PE 塑层,通过 1000 小时盐雾测试,在潮湿的食品加工车间使用 5 年无锈蚀,维护成本下降 40%。
四、如何筛选优质可移动车间隔离网厂家?这三个标准必须看
优先选择具备自主知识产权的厂家,如拥有 “快速拆装结构”“多向调节组件” 等专利(可在国家知识产权局查询)。某厂家因缺乏核心专利,产品在使用 3 个月后出现卡扣断裂,导致客户被迫整体更换。
重点考察汽车制造(需耐油污)、电子洁净车间(需防尘等级)、食品加工(需防腐)等细分领域案例。例如为海尔工厂、比亚迪车间提供过方案的厂家,技术成熟度更有保障。
- 看服务体系:是否提供 “测量 - 设计 - 调试” 全流程服务
优质厂家应配备专业 CAD 设计团队,可根据车间三维图纸提供定制方案,并支持现场试装。某医疗器械厂因厂家未提供测量服务,导致隔离网与消防栓位置冲突,返工损失达 8 万元。
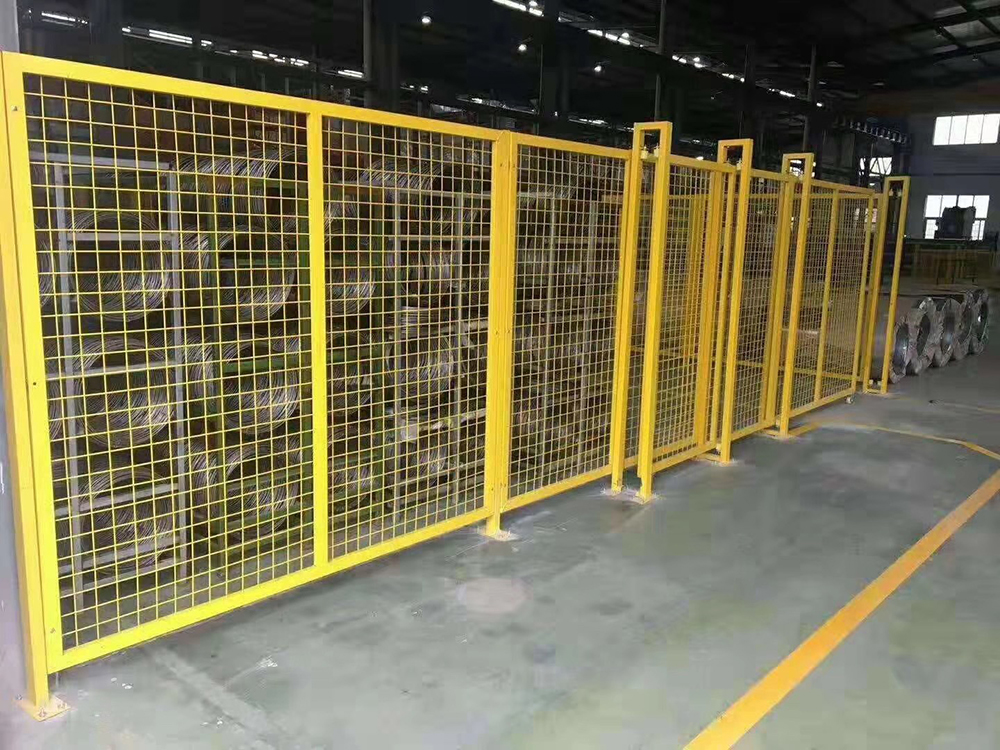
五、结语:可移动隔离网开启智能工厂柔性化转型之路
从 “固定分隔” 到 “动态适配”,可移动车间隔离网不仅是物理屏障,更是智能制造的基础设施。其价值不仅在于 70% 的安装效率提升,更在于:
- 成本可控:按需采购模块,避免过度建设,初期投资降低 25%;
- 响应敏捷:快速应对订单波动,小批量多品种生产模式下换线时间缩短 50%;
- 安全升级:标配防倾倒装置(倾斜角度>15° 自动锁死),符合 GB/T 3091-2015 工业护栏安全标准。
立即联系优质厂家:18703182863。获取免费车间布局设计方案,或下载《可移动隔离网选型参数表》,让柔性生产从 “区域隔离” 开始优化。选择专业厂家,就是选择降本增效的确定性!